 |
TECHNOLOGY
Our aim is to
employ the newest, most efficient mining equipment and methods as well
as recovery technologies. We will
carry out all aspects of the mining, from initial exploration to final
site reclamation and regeneration, with as little disruption to the
environment as possible. Ultimately, the total mining process will be beneficial
to the environment. Mining technology has advanced slowly in the
past and many things, believed to be impossible only decades ago, are
not only possible but viable today.
Our
Leading Edge “MR System”
M Quest has leading edge technology, the “MR System,” which, when fully
developed, will have the capability
of extracting more than 95% of all gold (coarse and fine) and
other precious, base and heavy metals from placer mines.
US$10 gold per
cubic yard placer ground (as tested by conventional methods), when processed with our MR System, will
potentially produce as high as US$40 per cubic yard gold equivalent.
How
It Works
The placer
pay-gravel is extracted from its natural in situ formation using heavy
equipment, placed onto the MR System where it is washed and then
classified. Gold and other precious, base and heavy (contaminant)
metals are recovered, and the gravels are returned damp/wet to within a
short distance of their original location. The washed barren gravel is
then contoured and any overburden and/or top soil is spread back on
top. The ground is either left to regenerate naturally or seeded per
expert advice.
All wash water used in our MR System is
contained within the system. It is cleaned and reused without the use
of chemicals anywhere in the system. Settling ponds will not be
used once we complete our Model “C” MR System.
The
Advantages
Our Model “C” MR System will be the only
system able to meet and exceed the stringent new regulations placed on
all placer mining in the Yukon as of November 2002. In addition,
it will recover in excess of 95% of
all the gold (coarse and fine) and other precious, base and
heavy metals from the pay-gravels.
We will have the ability to mine or reclaim mines
anywhere in the world at a low cost, even on poor ground. We
also will be able to recover far greater amounts of gold than the
original miners did with the then conventional technology.
Operational
Field Testing
Our
2001/02 Field Sampling and Road Upgrading
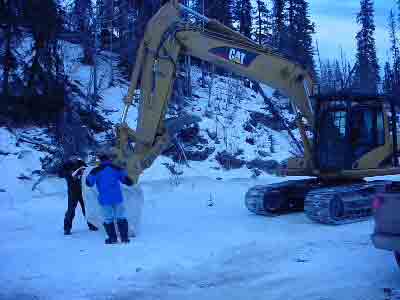
A testing program was carried out in December 2001 and
January 2002. The weather was extremely cold (-50C, -60F) making the
testing extremely difficult for men and machinery. The road upgrading
was completed by members of the Kluane First Nation in the beginning of
October 2001 just prior to the first snow.
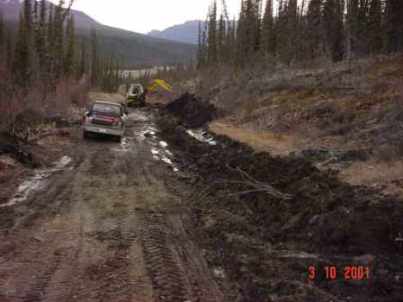
2003 Model “A” MRS Plant

The testing of the new technology was successful and has given us
extremely valuable information for our future designs. Moving from the
laboratory bench to field scale-up operations has its challenges at the
best of times. This is why we have chosen to do our scale-up through
the development of three models “A,” “B” & “C.”
During
the 2003 season our Model “A” MRS Pilot Plant, the forerunner of our MR
System, achieved some limited results in meeting the Mining Land Use
Standards. Toward the end of the season, when we had concluded our main
testing of the new technology, we began using small external settling
ponds to handle our wash water. We processed a large enough bulk sample
to assist us in the modification process from the Model “A” MRS Plant
to the Model “B” MR System and possibly onto the Model “C.”
When we operated and tested
the Model “A” MRS Plant during the 2003 season in the conventional
manner, we recovered, on average, US$10 gold per cubic yard of
processed gravels.
2004 Model “B” MR System
In 2004 we will
have the very latest state-of-the-art mineral processing plant—a
“modified conventional plant.” Our
first priority is to ensure that we clean the water and return the
mixed coarse and fine tailings to their original location.
We plan to
upgrade the fine and ultra-fine gold recovery sub-systems as we prove
and improve them. At a minimum, we are using a modified conventional
recovery system that has a proven track record and we are progressively
upgrading it until we reach the ultimate and final production models
that become our MR Systems. In very
short order, we will be in production with a stronger, more reliable
and much higher capacity mining system.
According
to our estimates, this modified conventional plant will produce at the
50% efficiency range and, with our water and fines/ultra-fines
technology, we will improve the
recovery efficiency up to 70% or 80%. This will be our Model “B”
MR System. We will further modify this unit to include clay processing
capability. After successful testing, we plan to relocate the system in
order to begin test mining operations on Fry Pan Creek.
The basic
components of the modified conventional plant will be a primary washing
unit, that will thoroughly wash both boulders and gravels, and a
primary classifier to handle the coarse feed material. The undersize
material and all wash water will go through further classifying
equipment and then over two 9-foot circular jigs. The underflow from
these 9-foot jigs will go to two 3-foot circular jigs and then to a
centrifuge. The concentrate from the centrifuge is then fed over shaker
tables to recover some of the finer gold and other precious, base and
heavy metals from these concentrates. All overflow material from each
step will be processed to recover the coarser gold and other metals. We
also will have added our technology to recover the fines and ultra
fines in addition to cleaning the water of all sediments and, in
particular, of metal toxins.
The Final Model “C” MR System
The Model “C” MR
System will be manufactured in various sizes to custom suit any
individual mine requirements.
The Model “C” MR System will be the
ultimate placer mining system and we will update it continually
with new technology until it is overtaken by the next paradigm shift in
mining technology. We plan to remain on the leading edge of
technological advancement and be the creators of, or at the very least,
be involved in the development of such technology.
|
 |